UKIRT
WFCAM - Optical Design
Optical
System Design Description
(WFCAM
Doc Number 3.1d020O, by David Henry - June 2002)
This
document describes the design of the optical system of the Wide
Field Camera (WFCAM) for the UK Infrared Telescope (UKIRT).
This
document contains the following:
·
A detailed description of the optical system
·
The performance of the optical system, in various
formats
·
The detailed prescription of the optical system
The
optical design of WFCAM is carried out using the Zemax optical design
programme. This document is based on design version WFCAM NEW
107.ZMX.
WFCAM
is a wide field imaging camera, primarily designed to carry out
large scale semi-automatic surveys of the sky. It operates in the
near IR (1-2.5mm).
It
uses 4 2048x2048 pixel focal plane arrays. These are arranged in
a 2x2 pattern, spaced by approximately 90% of a detector spacing.
Four separate stepped exposures are taken and combined to produce
a single image frame, covering approximately 0.9° x 0.9°.
Figure
1 shows the layout of the focal plane, together with the angular
field coverage of the optical system.
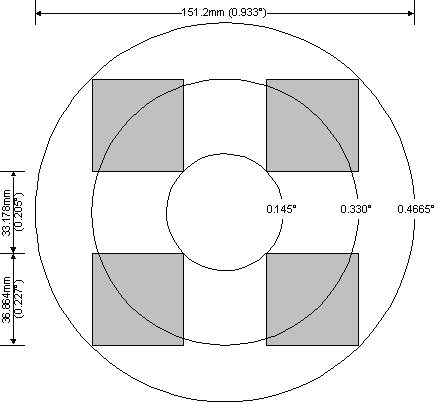
Figure
1 – WFCAM Focal Plane Layout
In
order to maximise survey speed a pixel scale of 0.4 arcsec/pixel
(22.22 arcsec/mm, 18mm pixel) has been chosen. This
gives a large field of view of 0.933° diameter. The optical system
has been designed for a field of view of 0.94° diameter, giving
a small margin over the required field of view.
The
optical design has a re-imaged pupil where a cold stop is located.
This stop minimises the thermal background to ensure maximum sensitivity
in the K band, and helps to control stray light.
WFCAM
has a number of interchangeable filters. The majority of the scientific
goals for the instrument will be fulfilled using Y, J, H and K broadband
filters. In addition, narrow band filters within this region may
also be used.
The
optical system has been optimised to give maximum performance in
the four broadbands. The wavelengths used in the design for each
of these wavebands are shown in Table 1 .
Waveband
|
Lower l
(mm)
|
Centre l
(mm)
|
Upper l
(mm)
|
Y
|
0.97
|
1.02
|
1.07
|
J
|
1.17
|
1.25
|
1.33
|
H
|
1.49
|
1.635
|
1.78
|
K
|
2.03
|
2.20
|
2.37
|
Table
1 - Wavebands
Figure
2 shows an optical layout of the WFCAM optical system. Figure 3
and Figure 4 show close-ups of the cryostat optics and detector
optics respectively.
Figure
2 – WFCAM Optical Layout
Figure
3 – Cryostat Optical Layout
Figure
4 – Detector Optical Layout
WFCAM
uses the existing UKIRT primary mirror. This forms the aperture
stop for the optical system. The following parameters for the primary
mirror are assumed (see AD1).
·
Diameter 3802.5mm
·
Focal length 9516mm
·
Conic constant -1
To
achieve the large required field of view, the WFCAM system uses
a new secondary mirror, giving an f/9 intermediate focus at around
5.7 metres in front of the primary mirror. The secondary mirror
is mounted on a fast 2-axis precision tip/tilt stage. This is in
turn mounted on a HEXAPOD stage, allowing precise movement of the
secondary mirror in 6 axes.
At
the intermediate focus, a large field lens is placed. This forms
an image of the entrance pupil (the primary mirror) inside the cryostat.
The lens is equi-convex.
The
next element in the beam is the cryostat window. This is a plane
parallel window.
The
next optical element is a corrector plate. One side of the plate
is flat, and the other side has an aspheric profile. It is similar
in shape to a Schmidt plate, but is not placed at a pupil image.
It therefore helps to correct off axis image quality (particularly
coma) as well as spherical aberration.
Inside
the cryostat an image of the primary mirror is produced by the field
lens. The cold stop is located here. The size and position of the
cold stop aperture are optimised for stray light rejection in the
K-band.
The
tertiary mirror is located at the rear of the cryostat. This converts
the f/9 beam from the secondary mirror into the f/2.44 beam required
to give the correct pixel scale. The tertiary mirror is a concave
ellipsoid.
The
beam then passes through the filters. Four separate filters are
used, one for each detector array. These are mounted in a mechanism
which allows them to be placed in the beam. Each filter is plane
parallel. A filter exchange mechanism selects the appropriate filter
for use, with the unused filters being stored out of the beam at
the side of the cryostat. The filters are discussed in more detail
below.
Directly
in front of the focal plane is a plano-concave fused silica field
flattening lens.
The
full optical prescription of the system is given in section 4.
All
refractive elements in the system are fabricated from Heraeus INFRASIL
302, an infrared grade fused silica. Figure 5 shows the typical
transmission of this material.
IR
grade fused silica gives excellent transmission at the wavelengths
of interest, together with extremely high refractive index uniformity.
This is an important consideration bearing in mind the large size
of some of the components.
Figure
5 – Transmission of Heraeus Infrasil
The
optical design chosen for WFCAM mounts the detector arrays in the
incoming beam. These therefore cause an obstruction in the beam,
leading to loss of image quality and throughput.
For
the purposes of calculating the baseline performance of the optical
system, the following obscurations are included in the optical system.
·
A circular hole (1m diameter) in the primary mirror
·
A square obscuration (142mm x 142mm) located at the
position of the filters, between the cold stop and the tertiary
mirror. This models the effect on the beam of the obstruction caused
by the filters and focal plane unit.
The
plot below shows the beam footprint on the front surface of the
filters (in J band). A beam is shown coming from the corner of each
detector, giving 16 beams in all.
Figure
6 – Filter footprints
From
this we can see that there is no overlap between the beams from
each separate detector. This allows the use of separate smaller
filters for each detector. The required beam size for each filter
is 52mm.
Table
2 gives the focal length and pixel scale of the optical system at
the centre wavelength of each waveband. Pixel scale is calculated
assuming an 18mm square pixel.
Waveband
|
Centre
l
(mm)
|
Focal
Length (mm)
|
Pixel
scale (arcsec/pixel)
|
Y
|
1.035
|
9265.971
|
0.40069
|
J
|
1.25
|
9271.198
|
0.40046
|
H
|
1.635
|
9278.419
|
0.40015
|
K
|
2.2
|
9281.900
|
0.40000
|
Table
2 – Focal length and pixel scale
Figure
7 shows the diffraction MTF of the system up to a spatial frequency
of 27 cycles/mm, in each of the wavebands. The specification frequency
for the MTF is at 1.2 cycles/arcsec (26.67 cycles/mm).
MTF
- Y Band
MTF - J Band
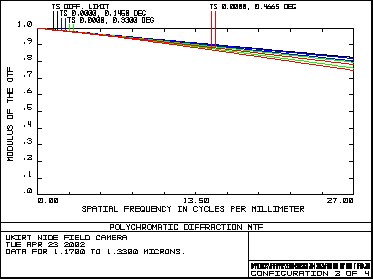
MTF
- H Band
MTF - K Band
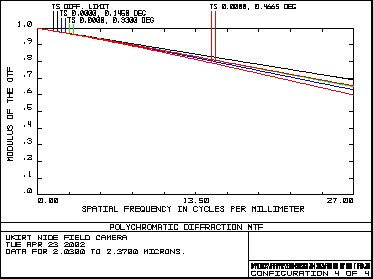
Figure
7 – MTF in Y,J, H and K bands
Figure 8 shows the variation of MTF (at 27 cycles/mm) with field
angle in each of the four wavebands. For each waveband, the plot
shows the sagittal (diamond), tangential (square) and average (solid)
MTF. The dashed line indicates the (on axis) diffraction limit for
each waveband.
Figure
8 – Variation of MTF with field angle
Figure
9 shows encircled energy radius plots for each of the four main
wavebands.
Encircled
Energy - Y Band
Encircled Energy - J Band
Encircled
Energy - H Band
Encircled Energy - K Band
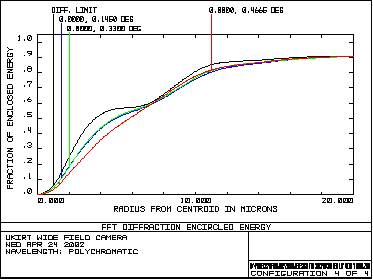
Figure
9 – Encircled energy in Y,J,H and K bands
Figure 10 shows the 50% and 80% encircled energy diameter (in arcsec)
as a function of field angle for each of the four main wavebands.
Figure
10 – Variation of encircled energy diameter with
field angle
Figure
11 shows the percentage optical distortion as a function of field
angle at the central wavelength of each of the four main wavebands.
Figure
11 – Variation of distortion with field angle
Figure
12 shows the OPD performance of the system in the four main wavebands.
OPD
- Y Band
OPD - J Band
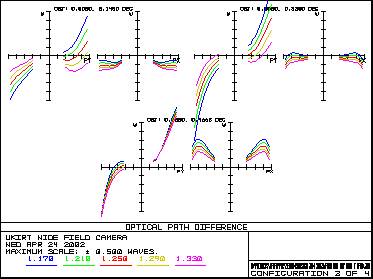
OPD
- H Band
OPD - K Band
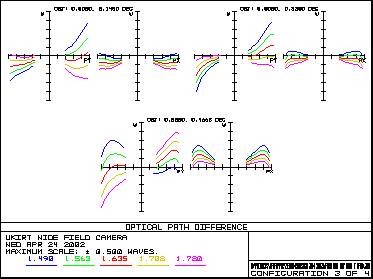
Figure
12 – Wavefront error in Y,J,H and K bands
The
coordinate system used is shown in Figure 13.
Figure
13 – WFCAM Coordinate System
The
origin of the coordinate system is at the pole of the primary mirror,
and the optical axis of the system lies along the Z-axis. Light
travelling from the sky towards the primary mirror is travelling
along the positive Z-axis. All dimensions are in mm.
The
baseline optical prescription is given in Table 3 .
Surface
|
Radius
|
Conic Constant
|
Glass
|
Thickness
|
Global Position
|
Primary Mirror
|
-19032
|
-1
|
|
-8655
|
0
|
Secondary Mirror
|
-2413.8
|
-3.61
|
|
2891
|
-8655
|
Field Lens (front)
|
1656
|
|
Infrasil
|
80
|
-5764
|
Field Lens (back)
|
-1656
|
|
|
2168
|
-5684
|
Window (front)
|
Flat
|
|
Infrasil
|
35
|
-3516
|
Window (back)
|
Flat
|
|
|
230
|
-3481
|
Corrector Plate (front)
|
6611.297953
|
|
Infrasil
|
35
|
-3251
|
Corrector Plate (back)
|
Flat
|
|
|
1016.1
|
-3216
|
Filter Obstruction
|
Flat
|
|
|
5.5
|
-2199.9
|
Cold Stop
|
Flat
|
|
|
1299
|
-2194.4
|
Tertiary Mirror
|
-2097.4
|
-0.069
|
|
-1304.5
|
-895.4
|
Filter (front)
|
Flat
|
|
Infrasil
|
-5
|
-2199.9
|
Filter (back)
|
Flat
|
|
|
-8.8
|
-2204.9
|
Field Flattener (front)
|
Flat
|
|
Infrasil
|
-10
|
-2213.7
|
Field Flattener (back)
|
-2093.5
|
|
|
-16
|
-2223.7
|
Detector
|
Flat
|
|
|
|
-2239.7
|
Table
3 – WFCAM Optical Prescription
Notes:
1)
All dimensions and parameters are at the nominal
operating temperature.
2)
Global positions indicate the location of the pole
of the surface along the Z axis.
The
beam diameter, clear aperture diameter and outside diameter for
each element is shown in Table 4
Surface
|
Beam
Diameter (1)
|
Clear
Aperture (2)
|
Outside
Diameter (3)
|
Notes
|
Primary
|
3800
|
3800
|
3800
|
|
Secondary
|
487.119
|
496
|
504
|
|
Field Lens (front)
|
534.560
|
539
|
560
|
|
Field Lens (back)
|
531.239
|
|
|
|
Window (front)
|
456.505
|
460
|
480
|
|
Window (back)
|
455.695
|
|
|
|
Corrector Plate (front)
|
448.053
|
450
|
490
|
|
Corrector Plate (back)
|
447.282
|
|
|
|
Tertiary Mirror
|
797.907
|
802
|
814
|
|
Filter (front)
|
50.9
|
53
|
55
|
(4)
|
Filter (back)
|
49.5
|
|
|
(4)
|
Field Flattener (front)
|
113.831
|
120
|
128
|
(5)
|
Field Flattener (back)
|
111.056
|
|
|
(5)
|
Table 4 – Optical element diameters
Notes:
1)
The beam diameter is the size of the nominal optical
beam on the surface
2)
The clear aperture is the minimum optical aperture
required, allowing for tolerance buildup, flexure, etc.
3)
The outside diameter is the physical size of the
component, allowing for mounting.
4)
Size of an individual square filter element – dimensions
are edge lengths
5)
Field flattener lens is square – dimensions are edge
lengths
The
front surface of the corrector plate is a high order aspheric surface.
The surface sag is described by the following equation:
z(r) surface sag at radial coordinate r
c surface curvature, c=1/radius of curvature
a2,a4,a6 aspheric
coefficients
Table
5 gives the coefficients of this surface at the nominal operating
temperature of 250K.
Parameter
|
Value
|
Radius
of curvature
|
6611.297953
|
R2
term
|
-5.3091568x10-5
|
R4
term
|
-2.3896351x10-10
|
R6
term
|
-1.9966489x10-16
|
Table
5 – Corrector plate aspheric coefficients (250K)
Figure
14 shows the profile of the surface sag, together with the deviation
of the aspheric profile from the best fit sphere.
Figure 14 – Corrector plate aspheric profile
Table
6 shows a table of the sag values against radius (at 250K).
Radius
|
Sag
|
Radius
|
Sag
|
Radius
|
Sag
|
0
|
0.0000
|
80
|
0.1344
|
160
|
0.4173
|
10
|
0.0023
|
90
|
0.1668
|
170
|
0.4473
|
20
|
0.0090
|
100
|
0.2013
|
180
|
0.4730
|
30
|
0.0201
|
110
|
0.2374
|
190
|
0.4933
|
40
|
0.0354
|
120
|
0.2745
|
200
|
0.5070
|
50
|
0.0548
|
130
|
0.3118
|
210
|
0.5128
|
60
|
0.0780
|
140
|
0.3486
|
220
|
0.5094
|
70
|
0.1047
|
150
|
0.3840
|
225
|
0.5037
|
Table
6 – Aspheric Profile Sag
To
achieve optimum performance, the optical system requires refocussing
of the secondary mirror and detector for each of the four main wavebands.
This is achieved using the secondary mirror collimation unit and
the detector focus mechanism.
The
main driver behind the incorporation of a detector focus mechanism
comes from the thermal design of the cryostat. As the thermal model
only predicts component temperatures to an accuracy of a few Kelvin,
it is difficult to design the optical system such that it will be
in focus at the operational temperature. Small errors in the predicted
temperature lead mainly to focus errors, which are easily corrected
with a focus mechanism. The incorporation of a detector focus mechanism
also allows the use of curvature sensing techniques.
The
focus mechanism moves the entire detector assembly, including the
field flattening lens. The optical effect is therefore a variation
of the distance between the filter surface and the field flattener.
Table
7 shows the position changes for the secondary mirror and the detector
focus mechanism.
|
M2 offset
|
Detector
Focus Offset
|
Band
|
Offset
|
Global
|
Offset
|
Global
|
Y
|
-1.41
|
-8653.59
|
+1.19
|
-2214.89
|
J
|
-0.77
|
-8654.23
|
+0.56
|
-2214.26
|
H
|
+0.21
|
-8655.21
|
-0.40
|
-2213.30
|
K
|
+0.31
|
-8655.31
|
-0.49
|
-2213.21
|
Table 7 – Nominal secondary mirror and focus mechanism
positions
Notes:
1)
Offsets are measured from the nominal positions listed in Table
3 .
2)
Positive offset is away from primary mirror, negative
is towards
3)
Detector focus global position refers to the pole of the front surface
of the field flattener
There
are two thermal effects which have an effect on the optical design;
the change in refractive index with temperature, and the change
in dimension with temperature.
The
nominal temperatures of each optical component are shown in Table
8
Component
|
Material
|
Nominal
Operating Temperature (K)
|
Secondary
Mirror
|
Zerodur
|
273
|
Field
Lens
|
Infrasil
|
273
|
Window
|
Infrasil
|
273
|
Corrector
plate
|
Infrasil
|
250
|
Tertiary
mirror
|
Zerodur
|
120
|
Filter
|
Infrasil
|
120
|
Field
flattener
|
Infrasil
|
70
|
Table
8 – Nominal operational temperatures
All
of the refractive elements in WFCAM are of infrared grade fused
silica (Heraeus Infrasil 302). Refractive index thermal variation
is accounted for by using different glass models to represent different
temperatures.
Data
for the room temperature (293K) refractive index is taken from the
Heraeus product catalogue. For calculation of the refractive index
at other temperatures, the room temperature data is scaled in accordance
with calculations in Matsuoka
[1] and Wray & Neu [2] .
Figure
15 shows the refractive index vs. wavelength for the Infrasil glass
models at the four temperatures used in the WFCAM design.
Figure 15 – Infrasil refractive index
The
models for 70K, 120K and 250K represent the absolute refractive
index (in vacuum) as they are used for lenses inside the cryostat.
The model for 0°C represents the relative refractive index (in air),
as it is used for elements outside the cryostat.
The
WFCAM optical system as designed is at nominal operating temperatures,
but all components are made and tested at room temperature. Dimension
changes with temperature are assessed by applying a thermal expansion
scaling to the operating temperature dimensions.
Data
for the thermal expansion coefficient of Zerodur and Infrasil are
taken from Englisch
[3] . Figure 16 shows the variation of thermal expansion
coefficient with temperature.
Figure
16 – Thermal expansion coefficient
Dimensional
changes are then given by:
where
D0 = dimension at operational temperature T0.
Table
9 shows the change in dimensions with temperature.
|
Operating
|
|
|
Operational
|
Room Temp
|
Component
|
Temp (K)
|
Material
|
Parameter
|
Value
|
Value (293K)
|
Secondary Mirror
|
273
|
Zerodur
|
Radius
|
-2413.8
|
-2413.799868
|
|
|
|
Conic Constant
|
-3.61
|
-3.6099998
|
Field Lens
|
273
|
Infrasil
|
Radius (F&B)
|
1656
|
1655.981533
|
|
|
|
Thickness
|
80
|
79.999108
|
Corrector Plate
|
250
|
Infrasil
|
Radius
|
6611.297953
|
6611.149013
|
|
|
|
Thickness
|
35
|
34.999212
|
|
|
|
A2
|
-5.3091568E-05
|
-5.309037E-05
|
|
|
|
A4
|
-2.3896351E-10
|
-2.389581E-10
|
|
|
|
A6
|
-1.9966489E-16
|
-1.996604E-16
|
Tertiary Mirror
|
120
|
Zerodur
|
Radius
|
-2097.4
|
-2097.430356
|
|
|
|
Conic Constant
|
-0.069
|
-0.069001
|
Filter
|
120
|
Infrasil
|
Thickness
|
5
|
4.999800
|
Field Flattener
|
70
|
Infrasil
|
Radius (back)
|
-2093.5
|
-2093.474842
|
|
|
|
Thickness
|
10
|
9.999880
|
Table 9 – Dimension changes with temperature
With
the exception of the corrector plate aspheric surface, all of these
changes are well within the tolerances specified on the parameters
(see AD2). Therefore, the values specified on the component drawings
are those of the nominal design at the operational temperatures.
As
the corrector plate aspheric profile is a nominal shape and is not
toleranced directly, the room temperature values for the radius
and the aspheric coefficients are specified on the corrector plate
drawing.
The
change from room (laboratory) temperature to operational temperature
changes the global position of the optical elements. A simple model
is used to estimate these changes, based on the materials used in
the instrument construction. The model calculates the global positions
of the optics at 20°C, and can then be cross checked
against more accurate thermal models.
Data
for the thermal contraction of the materials used in the instrument
is taken from the ATC materials database. Figure 17 shows the integrated
thermal contraction of the three main materials used (Aluminium,
Steel and G10 fibreglass).
Figure
17 – Integrated thermal contraction of materials
Figure
18 shows the simple thermal model used to calculate the changes
in global positions. For each components, the change in distance
for the surface vertex closest to the tertiary mirror is
calculated. Changes in optical component thickness with temperature
are ignored. All positions are measured relative to the pole of
the primary mirror.
Figure
18 – Simplified Thermal Model
Table
10 shows the estimated global positions at 20° C.
|
Global Position
|
|
Element
|
Oper. Temp.
|
20°C
|
Difference
|
Primary
Mirror
|
0.0
|
0.0000
|
0.0000
|
Secondary
Mirror
|
8655.0
|
8655.0000
|
0.0000
|
Field
Lens (front)
|
5764.0
|
5766.5992
|
2.5992
|
Field
Lens (back)
|
5684.0
|
5686.5992
|
2.5992
|
Window
(front)
|
3516.0
|
3517.7794
|
1.7794
|
Window
(back)
|
3481.0
|
3482.7794
|
1.7794
|
Corrector
Plate (front)
|
3251.0
|
3259.4811
|
8.4811
|
Corrector
Plate (back)
|
3216.0
|
3224.4811
|
8.4811
|
Filter
Obstruction
|
2199.9
|
2205.0254
|
5.1254
|
Cold
Stop
|
2194.4
|
2199.5072
|
5.1072
|
Tertiary
Mirror
|
895.4
|
896.2172
|
0.8172
|
Filter
(front)
|
2199.9
|
2205.0254
|
5.1254
|
Filter
(back)
|
2204.9
|
2210.0254
|
5.1254
|
Field
Flattener (front)
|
2213.7
|
2218.8710
|
5.1710
|
Field
Flattener (back)
|
2223.7
|
2228.8710
|
5.1710
|
Detector
|
2239.7
|
2244.9568
|
5.2568
|
Table
10 – Global positions at 20°C
|